Stories from the field 08
The construction of Southeast Asia's longest raw water transfer tunnel to alleviate water shortage problems in Kuala Lumpur
– How a Japanese general contractor successfully dug a tunnel under a Malaysian mountain range
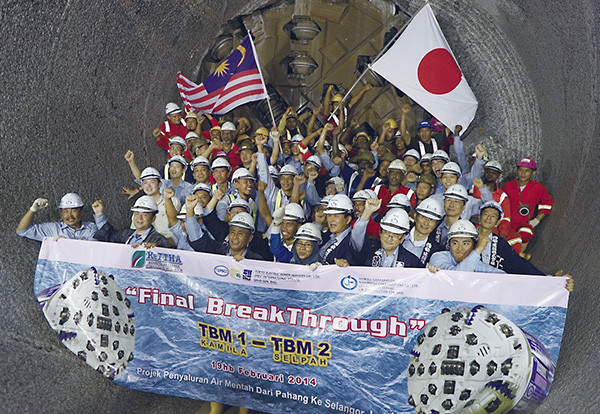
Workers celebrating the completion of the tunnel in front of a tunnel boring machine (TBM). (Photo: Shimizu Corporation)
Malaysia has been experiencing rapid economic growth since the 1980s. However, along with that growth, Malaysia's capital Kuala Lumpur, the center of commerce and industry in the country, has faced a major problem – there is not enough water for both daily life and industrial use. Development has been moving forward to ensure water resources in a river basin in Selangor State on the outskirts of Kuala Lumpur in order to deal with the city's rapidly increasing demand for water. However, efforts to secure resources had not always gone as planned, as demonstrated by such problems as the serious water shortage in the region for approximately half a year from 1997 to 1998.
The Malaysian government considered various plans to address this issue and eventually came to the conclusion that, from the perspective of the amount of water needed as well as cost, it would be best to channel water by digging a tunnel to the State of Selangor from the State of Pahang, a water-rich region in the central part of the Malay Peninsula.
Therefore, in June 2009, Malaysia began a project to build the Pahang-Selangor raw water transfer tunnel. It was to be one of the largest infrastructure projects in Asia – a 44.6 kilometers long, 5.2 meters in diameter tunnel with a water delivery capacity of 1.89 million cubic meters per day, laid underneath a mountain range between Pahang and Selangor States. For this project, Japan offered an ODA Loan covering 75% of the costs, and construction was undertaken by a joint venture established by Shimizu Corporation and Nishimatsu Construction Co., Ltd. from Japan and companies United Engineers Malaysia Berhad (UEMB) and IJM Corporation Berhad1 from Malaysia.
Recently, Japanese general contractors have embarked on large-scale development projects in the midst of the overseas construction booms. Mr. Takashi Kawata of Shimizu Corporation, who pulled a team together, was specially selected as a project manager for this big project in consideration of his proven track-record, including his contribution to the successful construction of an underground hydraulic power plant in Indonesia during the 1990s.
Construction began in September 2009. The tunnel construction was divided into eight sections. The construction team decided to use a tunnel boring machine (TBM) combined with the New Austria Tunneling Method (NATM), which uses dynamite, to penetrate tough bedrock underneath the mountain range. The project got off to a good start. The work for building a road to allow access of machinery and equipment to the site prior to excavation was completed ahead of schedule. However, once excavation started, the construction team ran into various unexpected issues. For instance, at one point, the workers uncovered a massive, empty cavern inside a mountain, over 50 meters high. At another point, they ran into pressurized spring water that shot out as much as 24.6 tons of water per minute. Another time, the main bearing, the central part of the TBM, broke after a rock burst when the machine was digging through a tough slab of granite. The unrelenting power of nature forestalled the project's progress again.
Looking back on the many difficulties the project faced, Mr. Kawata commented, “It was a difficult work environment. Under a long mountain range, we had to dig a tunnel 5 kilometers long over 1,000 meters underground, which by itself was a hard task. In addition to high temperature and humidity, we ran into a place where the temperature of the bedrock we were digging, and the water that gushed out of it exceeded 50°C.”
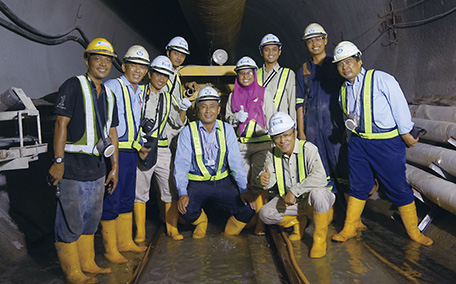
With the workers from around the world. Mr. Takashi Kawata (center). (Photo: Shimizu Corporation)
The project was able to overcome these challenges thanks to the strong solidarity of its multinational team consisting of over 1,000 people from 15 countries who united and tackled problems with single-minded dedication. Every day, Mr. Kawata instructed his workers to keep their worksite tidy and safe, with not even a single piece of scrap wire lying about. He made a point of fully tidying up the site himself and greeting others with a smile in order to set an example of expected behaviors and encourage his workers to act the same.
“Just after construction began, an assistant project manager of a local Malaysian company that was participating in the joint venture told me that if I was always nagging, pretty soon we would not have any workers left. I told him that if people were going to quit over something like that, I would not mind. In the end, none of our contractors quit. And I have heard that the assistant manager is now using my management method in his current project.”
Even employees for whom it was initially difficult to adjust to Japanese methods began to slowly change their attitudes as they understood that maintaining a tidy and pleasant worksite would lead to greater safety and efficiency.
This huge excavation project was completed in February 2014, just four years and nine months after it started. That such a difficult construction project could be completed without any injuries goes to show yet again how effective the general contractors who supported Japan's period of high economic growth are, with respect to both their technology and attitude towards creating a safe worksite.
*1 IJM Corporation Berhad (A joint venture of IGB Construction Sdn Bhd, Jurutama Sdn Bhd, and Mudajaya Sdn Bhd)
<< Previous Page Next Page >>
Main Text | Statictics and Reference Materials | Stories from the field | Master Techniques, From Japan to the World - | ODA Topics