Master Techniques from Japan to the World 6
Creating New Business in
South Africa through Waste
Plastic-to-Oil Conversion
– Japanese companies creating electricity and employment
from waste plastic
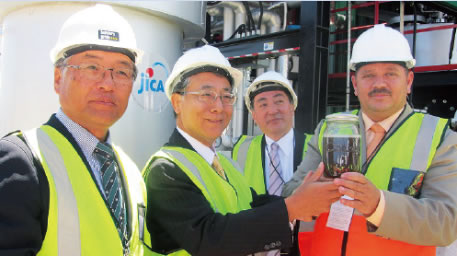
From the left is Mr. Tetsuya Sato of CFP Corporation, Mr. Shigeyuki Hiroki, Ambassador of Japan to South Africa, Mr. Hiroyuki Kinomoto, JICA South Africa Director, and Mr. Ernest Sonnenberg, Councillor of Capetown City. They are holding a jar of crude oil. (Photo: CFP Corporation.)
The Republic of South Africa possesses a wealth of mineral resources and the mining industry has historically been one of the mainstays of its economic growth. However, in 2015, GDP breakdown by industry group showed that tertiary industries1 account for 69% of economic output. Furthermore, it showed that the manufacturing and financial industries in South Africa are developing, and that South Africa is continuing its growth towards becoming a mid- to high-income country and becoming a driver for the African economy as a whole. Unfortunately, although people’s lives are becoming more affluent, volumes of general waste2 are increasing every year, making recycling of such waste materials a challenge. Waste plastics account for 60% of all general waste and recycling efforts have made little progress. The Government of South Africa has set a recycling target rate of 25% for waste plastic, but the actual rate remains low at around 18%. Almost all waste plastic is directly dumped in waste disposal facilities.
It is hoped that the waste plastic-to-oil production system developed by CFP Corporation3 (Fukuyama City, Hiroshima Prefecture) will contribute to solving this waste problem. In the material recycling4 process it is difficult to recycle plastics, such as vinyl bags, that have food remains or dirt attached. Furthermore, the oil produced using conventional waste plastic-to-oil production equipment solidifies at low temperatures, so there was a difficulty in using such oil as fuel.
CFP Corporation tried to address this problem by combining a washing machine produced by KANEMIYA Co., Ltd.5 (Handa City, Aichi Prefecture) to its waste plastic-to-oil production system and it became possible to also use dirty waste plastic in the waste plastic-to-oil production process as a raw material. Another distinctive characteristic of the process is that CFP Corporation uses its own patented technology to ensure that recycled oil produced does not solidify, even at temperatures below 0℃. The system developed by CFP Corporation is capable of producing6 4,000 liters of oil per day. However, the pilot plant produces a maximum of 500 liters of recycled oil per day from 500 kg of waste plastic, which can then be used as fuel in diesel generators. The electricity generated can be used as the power for the waste plastic-to-oil production system so it possible to significantly reduce CO2 emissions compared to simply incinerating waste.
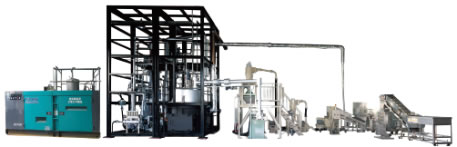
Composition of pre-treatment equipment and waste plastic-to-oil production system (Photo: CFP Corporation)
Working together to confirm the compatibility of the waste plastic-to-oil production system with local conditions, CFP and Kanemiya implemented the diffusion and verification survey7 from March, 2014 at Cape Town in South Africa with the private sector for the Disseminating Japanese Technologies in ODA project as part of JICA’s Partnership with Japanese SMEs.8 Cape Town was chosen as the location for the project because it is one of the few cities in South Africa that engage in waste separation and collection. Therefore, an environment was already in place for acquiring waste plastic as the raw material for the production process relatively easily.
In October 2015 the waste plastic-to-oil production system was installed at a waste management facility in Cape Town. Performance tests were conducted together with local staff members, who also showed their technical progress, and finally the local staff members were able to operate the system stably to the same level as Japan. Furthermore, the oil produced was used as fuel in diesel generators, as burner fuel in the production system, and as fuel for fork lift trucks. It was confirmed that the electricity generated from this fuel could be used to operate the system.
Mr. Tetsuya Sato, General Manager of the Overseas Marketing Department, Waste Management Division at CFP, says, “I hope that we can help to reduce waste, improve recycling rates, and contribute to building a sustainable waste management and recycling system, by introducing this production system.” Given South Africa’s chronic power shortage and expanding income disparity, Mr. Sato adds, “Not only does our waste plastic-to-oil production system help to supplement power shortages, it should also be able to create employment in a new recycling business.”
Following the conclusion of the diffusion and verification survey in September 2016, the production system used in the survey was presented to the Cape Town city authorities. It remains in use and is operated by a private company in the city. Mr. Sato is full of enthusiasm when he says, “Waste recycling is a common challenge for all developing countries. Using the results of this diffusion and verification survey as an example, we want to introduce waste plastic-to-oil production systems in other countries in Africa.”
Both CFP and Kanemiya exhibited at a side event held in conjunction with the Sixth Tokyo International Conference on African Development (TICAD VI), and introduced their waste plastic-to-oil production system to representatives of other African countries. As momentum gathers in Japan’s cooperation to Africa, both companies started on further expanding their business activities.
*1 Tertiary industries include electricity, gas, waterworks, transportation, communications, retail/wholesale, food and beverage, financial, insurance, real estate, services, and public services, among others. (Primary industries are agriculture, forestry, and fisheries, and secondary industries are mining, construction, and manufacturing.)
*2 General waste refers to all waste other than industrial waste.
*3 CFP Corporation developed a waste plastic-to-oil production system capable of producing oil by crushing, melting, and heat-decomposing waste plastics (polypropylene, polyethylene and polystyrene, etc.). The oil produced can be used as fuel in diesel generators and boilers, among other equipment.
*4 Material recycling refers to a recycling process in which waste plastic produced from used products or generated from production process are processed for use as materials for new products or as raw materials.
*5 KANEMIYA Co., Ltd., has developed a small-size, low-cost machine capable of washing waste plastic such as plastic bags that have food remains or dirt attached, which could previously not be used for recycling.
*6 One liter of recycled oil is produced from 1 kg of waste plastic.
*7 A survey to verify ways to enhance a product and technology’s compatibility with a developing country and thereby disseminate the product and technology, based on a proposal from a Japanese SME.
*8 Projects aiming to achieve both the development of developing countries and the activation of the Japanese economy by utilizing Japanese SMEs‘ excellent products and technologies through ODA.
<< Previous Page
Main Text | Statistics and Reference Materials | Stories from the Field | Master Techniques from Japan to the World | ODA Topics