Stories from the Field 3
Forging a Path to Ethiopia’s Future with “KAIZEN”
—Utilizing Japan’s strengths in combining technical cooperation and grant aid to maximize a synergistic effect—
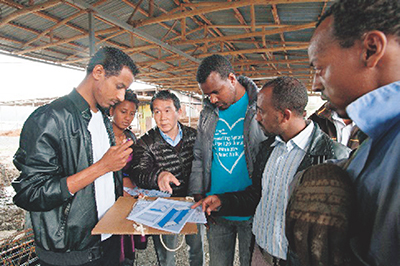
Mr. Sugimoto, a Japanese expert, discussing with his Ethiopian counterparts and company representatives at a construction materials factory (February 2013) (Photo: Japan Development Service Co., Ltd.)
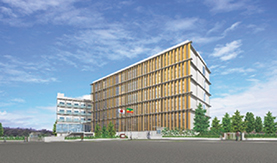
Conceptional image of the completed TICAD Human Resource Development Center for Business and Industry (Construction: Fujita Corporation; equipment procurement: Sirius Corporation) (Designed by the Consortium of Nippon Koei Co., Ltd. and Koei Research & Consulting Inc.)
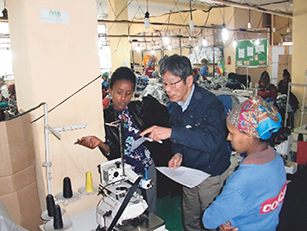
A Japanese expert giving guidance on “KAIZEN” for the manufacturing process on-site at a sewing factory (Photo: Japan Development Service Co., Ltd.)
In Ethiopia, located in the eastern part of Africa, cooperation through JICA began in 2009, focusing on the “KAIZEN”* method from Japan in order to enhance the competitiveness of Ethiopia’s domestic industries, such as the manufacturing industry. The Ethiopian Kaizen Institute (EKI) was established by the efforts of the late Prime Minister Meles Zenawi. Japan’s cooperation started with EKI as a foothold by promoting technical cooperation initiatives to transfer technical skills and experience through training and “KAIZEN” practice at factories, in order to popularize the “KAIZEN” approach within Ethiopia.
As a result of this cooperation, the concept is currently widely recognized across Ethiopia, and the certification, accreditation and registration system for consultants who provide training and guidance on “KAIZEN” for Ethiopian companies has been introduced. EKI, which started with only nine staff members at the time of its establishment, has increased its staff to approximately 110 consultants, and is spreading “KAIZEN” to many Ethiopian companies. In addition, cooperation is currently underway to ensure that EKI can disseminate “KAIZEN” through its Ethiopian staff even after the Japanese experts return to Japan.
Mr. SUGIMOTO Seiji of Japan Development Service Co., Ltd. (JDS), who led the initiative as a technical cooperation expert and Chief Adviser from 2011 to 2020, says, “It is not uncommon to see an increase in productivity of 30 to 50% in our indicators. Future challenges include disseminating “KAIZEN” to schools and ministries, introducing “KAIZEN” in management strategies and marketing for businesses, and further spreading the “KAIZEN” method not only to the capital area, but also across the entire country.”
In addition to the manufacturing industry, the Ethiopian government also hopes to disseminate “KAIZEN” to the service industry, and is currently providing training by EKI consultants to government-affiliated public corporations from the transportation sector. As a result, a significant outcome is expected in terms of cost reduction of approximately 100 million yen per year by thoroughly implementing 5S and reviewing the combinations of transportation routes and measures.
Since EKI did not previously have its own facilities and its consultants were directly visiting the factories and companies where training was taking place to give guidance on an individual basis, EKI’s activities were limited to the area around the capital Addis Ababa. The TICAD Human Resource Development Center for Business and Industry, which is currently in the process of construction and procurement of equipment through grant aid, is designed to resolve this issue and further promote the spread of “KAIZEN” throughout Ethiopia. The center, which is under construction close to the African Union (AU) headquarters, is planned to be equipped with training and accommodation facilities in addition to the EKI head office, where trainees from outside the capital will be able to stay and receive training.
Mr. HOSHIAI Yoshifumi from the Consortium of Nippon Koei Co., Ltd. and Koei Research & Consulting Inc., which is designing and supervising the construction of the center, tells us the following. “After the center is complete, it will be possible to accept up to approximately 12,000 trainees a year. While construction was temporarily suspended due to COVID-19, we hope that it will be finished as soon as possible, which will lead to the development of human resources and the development of Ethiopia as a whole.”
The Ethiopian government has set its sights on using the Center not only as a national training facility, but also for spreading “KAIZEN” to neighboring countries. As one of Africa’s core bases for human resources development, the center plans to accept trainees from neighboring countries. Japan’s consistent cooperation over the last decade has borne fruit, and the Japanese style “KAIZEN” initiatives are steadily taking root in the African continent.
*An approach in which each worker at a production site comes up with and implements their own ideas on how to eliminate inefficiency in the production process and improve quality and productivity. In Japan, in a period of rapid growth after WWII, this approach was cultivated on-the-job by the manufacturing industry to increase quality and productivity, and is based on 5S: “Sort, Set, Shine, Standardize, and Sustain.”
<< Previous Page Next Page >>
Main Text | Reference Statistics | Reference Materials | Stories from the Field | Master Techniques from Japan to the World | ODA Topics